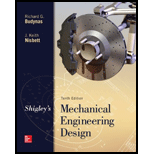
Concept explainers
The factor of safety using distortion energy theory.

Answer to Problem 75P
The factor of safety using distortion energy theory for inner radius is
The factor of safety using distortion energy theory for outer radius is
Explanation of Solution
Write the expression for contact pressure.
Here, the contact pressure is
Write the expression for inner radius.
Here, the inner radius is
Write the expression for outer radius.
Here, the outer radius is
Write the expression for tangential stress at outer radius for inner member.
Here, the tangential stress at outer radius for inner member is
Write the expression for tangential stress at inner radius for inner member.
Here, the tangential stress for inner member is
Write the expression for radial stress at outer radius for inner member.
Here, the radial stress for inner member is
Write the expression for second moment of area.
Here, the second moment of area is
Write the expression for stress.
Here, the stress in
Write the expression for second polar moment of area.
Here, the second polar moment of area is
Write the expression for shear stress.
Here, the shear stress is
Write the expression for von Mises stress for inner radius.
Here, the von Mises stress is
Calculate factor of safety for inner radius.
Here, the factor of safety for outer radius is
Write the expression for von Mises stress for outer radius.
Here, the von Mises stress for inner radius is
Calculate the factor of safety for outer radius.
Here, the factor of safety for outer radius is
Write the expression for nominal radius.
Here, the nominal radius is
Conclusion:
Substitute
Substitute
Substitute
Substitute
Substitute
The radial stress for inner radius is zero at inner member.
Substitute
Substitute
Substitute
Substitute
Here, the stress in outer member is
Substitute
Substitute
Here, the stress for inner member is
Substitute
Substitute
Substitute
Here, the shear stress for outer member is
Substitute
Substitute
Here, the shear stress for inner member is
Substitute
Substitute
Substitute
Thus, the factor of safety for outer radius is
The following diagram shows the 3D stress for outer radius.
Figure (1)
Substitute
Substitute
The value of
Substitute
Thus, the factor of safety for outer radius is
Want to see more full solutions like this?
Chapter 5 Solutions
Shigley's Mechanical Engineering Design (McGraw-Hill Series in Mechanical Engineering)
- , Solve the preceding problem using the numerical data: /) = 90mm, h = 280 mm, d = 210 mm, q = 14 kN/m, and L = L2 m.arrow_forwardRepeat Problem 3.3-1, but now use a circular tube with outer diameter d0= 2.5 in. and inner diameter di= 1.5 in.arrow_forward950 mm is employed to compress à 6061-T6 aluminum 650 mm as shown. The tie rod has a solid circular cross section with A solid 4340 HR Steel tie rod of length Lrod bushing of length Lbushing diameter drod do - = = 27.5 mm. The bushing has a hollow circular cross section with outer diameter 80 mm, inner diameter di, and wall thickness t. If F = 47.5 kN, determine the minimum wall thickness of the bushing based on the below design requirements: ⚫ the displacement of the bottom of the tie rod with respect to the fixed horizontal surface may not exceed total = 1.1 mm ⚫ the normal stress of the bushing may not exceed the yield strength of the bushing material tmin Lbushing do Lrod = 7.056 drod F Rod cross section drod Bushing cross section mm X 0% do diarrow_forward
- A safety valve spring made of oil-tempered chrome vanadium steel having a 9.5 coils has squared and ground ends. The outside diameter is 115 mm and wire diameter is 13 mm. It has a free length of 203 mm. The spring must be initially compressed to hold the boiler pressure of 1.38 Mpa on the valve seat of 32 mm diameter. Determine the spring stress if it is compressed to its solid length.arrow_forwardSolve Prob. 9–7 using the stress transformation equations developed in Sec. 9.2.arrow_forward4. The compression load of 120 kN acts on the steel pipe of Table B-14. Determine the minimum Nominal dimeter pipe when the safety factor is 1.5 with a yield strength of 240MPa.arrow_forward
- A machinery uses a helical tension spring with wire diameter of 3 mm and coil outside diameter of 35 mm. The spring has 9 total coils. The design shear stress is 500 MPa and the modulus of rigidity is 82 GPa. Determine the force that causes the body of the spring to its shear stress in N. Consider ground ends.arrow_forwardThe angle embraced is 175° and the coefficient of friction between the belt and the pulley is 0.25. A leather belt is required to transmit 9.5 kW from a pulley 100 cm in diameter, running at 2500 r.p.m.. If the safe working stress for the leather belt is 2 MPa, density of leather 1000 Kg/m³ and thickness of belt 1 cm, determine the width of the belt. Rim of plate Splined Sleeve Driving Shuff Dhe 11 Doc-A Thiven Shuffarrow_forward6-56 In the figure shown, shaft A, made of AISI 1020 hot-rolled steel, is welded to a fixed support and is subjected to loading by equal and opposite forces F via shaft B. A theoretical stress-concentration factor K„ of 1.6 is induced in the shaft by the -in weld fillet. The length of shaft A from the fixed support to the connection at shaft B is 2 ft. The load F cycles from 150 to 500 lbf. (a) For shaft A, find the factor of safety for infinite life using the Goodman fatigue failure criterion. (b) Repeat part (a) using the Gerber fatigue failure criterion. in dia Phoblem 6-56 I in 1 in -in fillet Shaft A Shaft Barrow_forward
- The 53kg girl shown is doing a chin-up. For the position shown, the humerous is modelled as an axially loaded member. Determine the normal stress (in MPa) at section a-a if the section is modelled as a hollow cylinder of outside diameter 22.4mm and inside diameter 15.2mm. Note: Do NOT include units in your answer a-+-a (а) (b) Answer:arrow_forwardUr: T 5-26. A cylindrical spring consists of a rubber annulus bonded to a rigid ring and shaft. If the ring is held fixed and a torque T is applied to the shaft, determine the maximum shear stress in the rubber. ľo Prob. 5-26 1 rod and the tube are made of 01 MP9 and tharrow_forwardThe connecting rod of a four stroke cycle Diesel engineis of circular section and of length 550 mm. The diameter and stroke of the cylinder are 150 mm and240 mm respectively. The maximum combustion pressure is 4.7 N/mm2. Determine the diameter ofthe rod to be used, for a factor of safety of 3 with a material having a yield point of 330 MPa.Find also the maximum bending stress in the connecting rod due to whipping action if the engine runsat 1000 r.p.m. The specific weight of the material is 7800 kg/m3. [Ans. 33.2 mm ; 48 MPa]arrow_forward
- Mechanics of Materials (MindTap Course List)Mechanical EngineeringISBN:9781337093347Author:Barry J. Goodno, James M. GerePublisher:Cengage Learning
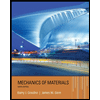