(a)
The force vs. reduction in height curve in open die forging of cylinder for
(a)

Explanation of Solution
Given:
The initial thickness of the specimen is
The initial diameter of the specimen is
The friction coefficient is
The velocity of the hydraulic press is
Formula used:
The expression for the flow stress is given as,
Here,
The expression for the true strain is given as,
Here,
The expression for the final radius by equating the volume is given as,
The expression for the forging force is given as,
Here,
The expression for the average pressure is given as,
The expression for final height for
The expression for final height for
The expression for final height for
The expression for final height for
The expression for final height for
Calculation:
For
The final height can be calculated as,
The final radius can be calculated as,
The true strain can be calculated as,
The flow stress can be calculated as,
Refer to table 2.2 “Typical values of strength coefficient
The average pressure can be calculated as,
The forging force can be calculated as,
For
The final height can be calculated as,
The final radius can be calculated as,
The true strain can be calculated as,
The flow stress can be calculated as,
Refer to table 2.2 “Typical values of strength coefficient
The average pressure can be calculated as,
The forging force can be calculated as,
For
The final height can be calculated as,
The final radius can be calculated as,
The true strain can be calculated as,
The flow stress can be calculated as,
Refer to table 2.2 “Typical values of strength coefficient
The average pressure can be calculated as,
The forging force can be calculated as,
For
The final height can be calculated as,
The final radius can be calculated as,
The true strain can be calculated as,
The flow stress can be calculated as,
Refer to table 2.2 “Typical values of strength coefficient
The average pressure can be calculated as,
The forging force can be calculated as,
For
The final height can be calculated as,
The final radius can be calculated as,
The true strain can be calculated as,
The flow stress can be calculated as,
Refer to table 2.2 “Typical values of strength coefficient
The average pressure can be calculated as,
The forging force can be calculated as,
For
Reduction (in | Forging force (in |
The plot between forging force and reduction in height is shown in figure (1) below,
Figure (1)
(b)
The force vs. reduction in height curve in open die forging of cylinder for
(b)

Explanation of Solution
Given:
The initial thickness of the specimen is
The initial diameter of the specimen is
The friction coefficient is
The velocity of the hydraulic press is
Formula used:
The expression for the flow stress is given as,
Here,
The expression for the true strain is given as,
Here,
The expression for the final radius by equating the volume is given as,
The expression for the forging force is given as,
Here,
The expression for the average pressure is given as,
The expression for final height for
The expression for final height for
The expression for final height for
The expression for final height for
The expression for final height for
Calculation:
For
The final height can be calculated as,
The final radius can be calculated as,
The true strain can be calculated as,
The flow stress can be calculated as,
Refer to table 2.2 “Typical values of strength coefficient
The average pressure can be calculated as,
The forging force can be calculated as,
For
The final height can be calculated as,
The final radius can be calculated as,
The true strain can be calculated as,
The flow stress can be calculated as,
Refer to table 2.2 “Typical values of strength coefficient
The average pressure can be calculated as,
The forging force can be calculated as,
For
The final height can be calculated as,
The final radius can be calculated as,
The true strain can be calculated as,
The flow stress can be calculated as,
Refer to table 2.2 “Typical values of strength coefficient
The average pressure can be calculated as,
The forging force can be calculated as,
For
The final height can be calculated as,
The final radius can be calculated as,
The true strain can be calculated as,
The flow stress can be calculated as,
Refer to table 2.2 “Typical values of strength coefficient
The average pressure can be calculated as,
The forging force can be calculated as,
For
The final height can be calculated as,
The final radius can be calculated as,
The true strain can be calculated as,
The flow stress can be calculated as,
Refer to table 2.2 “Typical values of strength coefficient
The average pressure can be calculated as,
The forging force can be calculated as,
For
Reduction (in | Forging force (in |
The plot between forging force and reduction in height is shown in figure (2) below,
Figure (2)
Want to see more full solutions like this?
Chapter 6 Solutions
EBK MANUFACTURING PROCESSES FOR ENGINEE
- A cylindrical billet that is 80 mm long and 32 mm diameter is reduced by backward extrusion to a 12 mm diameter. Half die angle is 90°. If the Johnson equation has a= 0.8 and b= 1.2 , and the flow curve for the work material has strength coefficient is 500 MPa, and strain hardening exponent is 0.8, Determine (a) extrusion ration, (b) true strain, (c) extrusion strain, (d) ram pressure, and (e) ram force.arrow_forwardA solid cylindrical slug made of 304 stainless steel is 150 mm in diameter and 100 mm high. It is reduced in height by 50% at room temperature by opendie forging with flat dies. Assuming that the coefficient of friction is 0.2 and the flow stress of this material is 1000 MPa, calculate the forging force at the end of the stroke. Manufacturing processesarrow_forwardA cylindrical part is warm upset forged in an open die. The initial diameter is 50 mm and the initial height is 40 mm. The height after forging is 30 mm. The coefficient of friction at the die-work interface is 0.25. The yield strength of the work material is 285 MPa, and its flow curve is defined by a strength coefficient of 600 MPa and a strain-hardening exponent of 0.12. Calculate the strain at yield point.arrow_forward
- During a direct extrusion process for a billet with 5 in long and diameter 2.5 in to 1.6 in. For the work metal, strength coefficient is 75000 Ib/in, and strain hardening exponent is 0.4, also the die angle of extrusion is 90. In Johnson extrusion strain equation a = 0.8, and b= 1.5. Determine: (a) extrusion ratio (b) true strain (c) extrusion strain, and (d) ram pressure at length 5, 4.2, 2.3,1.5,and 0 in.arrow_forwardAn open die forging operation is performed to produce a steel cylinder with a diameter of 9.7mm and a height of 1.7mm. The strength coefficient for this steel is 500MPA, and the strain hardening exponent is 0.25. Coefficient of friction at the die-work interface is 0.12. The initial stock of raw material has a diameter of 5mm. (a) What height/length of stock is needed to provide sufficient volume of material for this forging operation? (b) Compute the maximum force that the punch must apply to form the head in this open- die operation.arrow_forward5) A steel specimen of rectangular cross section with 120 mm width, 180 mm thickness and 90 mm height was upset at room temperature by open-die forging to a height of 55 mm. If the strength coefficient and strain hardening exponent of this material were 1015 MPa and 0.17 respectively, the coefficient of friction is 0.2, and assuming that the thickness would not change during forging; determine the required upsetting force at the end of stroke.arrow_forward
- A spool of wire has a starting diameter of 2.5 mm. It is drawn through a die with an opening that is 2.1 mm at a speed of 0.3 m/s. The worked metal has a strength coefficient of 450 MPa and a strain-hardening coefficient of 0.26. Assume the drawing is performed at room temperature and that the frictional and redundant work together constitute 35% of the ideal work of deformation. Calculate the power required to carry out the operationarrow_forwardA upset forging operation is performed in an open die. The initial size of the workpart is: Do = 63 mm, and ho = 100 mm. The part is upset to a diameter = 70 mm. The work metal has a flow curve with strength coefficient = 600 MPa and strain hardening exponent= 0.22. Coefficient of friction at the die-work interface = 0.40. Determine (a) final height of the part, and (b) maximum force in the operationarrow_forwardIn open-die forging, a disc of diameter 200 mm and height 60 mm is compressed without any barreling effect. The final diameter of the disc is 400 mm. The true strain isarrow_forward
- You have been asked to work on some design problems and technically support the team working on extrusion and forging operations: 1) The team are extruding a billet that is 80 mm long with diameter of 40 mm is directly to a diameter of 20 mm. The extrusion die has a die angle of 75°, see Figure 1. For the work metal, K = 600 MPa and n = 0.25. In the Johnson extrusion strain equation, a = 0.8 and b = 1.4. Remaining billet length 75 Ram pressure, p D. Dr Figure 1: Extrusion process. Determine the following design parameters: (a) Extrusion ratio. (b) True strain (homogeneous deformation). (c) Extrusion strain. (d) Ram pressure at L= 80, 40, and 10 mm. (e) Draw the relationship between the ram pressure and billet length and discuss the results. What are your recommendations to dccrcase the required ram pressure?arrow_forward* A cylindrical workpiece made of 1100-0 Aluminum that is 18 in high and 16 in in diameter and is to be reduced in height by 25% by open-die forging. Let the coefficient of friction be 0.15. K=20 mpa,n=0.35, Calculate the forging force.arrow_forwardEstimate the power for annealed low carbon steel strip 200 mm wide and 10 mm thick, rolled to a thickness of 6 mm. The roll radius is 200 mm, and the roll rotates at 200 rev/min; use coefficient of friction at the die-work interface (p)=0.1. A low carbon steel such as AISI 1020 has K (strength coefficient) = 530 MPa and n ( strain hardening exponent) =0.26a)1059 kWb)950 kWc)1183 kWd)875 kWarrow_forward
- Elements Of ElectromagneticsMechanical EngineeringISBN:9780190698614Author:Sadiku, Matthew N. O.Publisher:Oxford University PressMechanics of Materials (10th Edition)Mechanical EngineeringISBN:9780134319650Author:Russell C. HibbelerPublisher:PEARSONThermodynamics: An Engineering ApproachMechanical EngineeringISBN:9781259822674Author:Yunus A. Cengel Dr., Michael A. BolesPublisher:McGraw-Hill Education
- Control Systems EngineeringMechanical EngineeringISBN:9781118170519Author:Norman S. NisePublisher:WILEYMechanics of Materials (MindTap Course List)Mechanical EngineeringISBN:9781337093347Author:Barry J. Goodno, James M. GerePublisher:Cengage LearningEngineering Mechanics: StaticsMechanical EngineeringISBN:9781118807330Author:James L. Meriam, L. G. Kraige, J. N. BoltonPublisher:WILEY
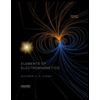
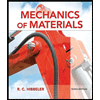
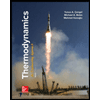
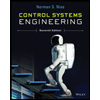
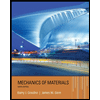
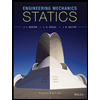