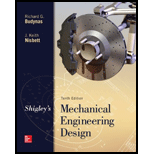
Concept explainers
A shaft is loaded in bending and torsion such that Ma = 70 N · m, Ta = 45 N · m, Mm = 55 N · m, and Tm = 35 N · m. For the shaft, Su = 700 MPa and Sy = 560 MPa, and a fully corrected endurance limit of Se = 210 MPa is assumed. Let Kf = 2.2 and Kfs = 1.8. With a design factor of 2.0 determine the minimum acceptable diameter of the shaft using the
(a) DE-Gerber criterion.
(b) DE-ASME Elliptic criterion.
(c) DE-Soderberg criterion.
(d) DE-Goodman criterion.
(a) Discuss and compare the results.
(a)

The diameter of shaft of shaft using DE-Gerber criterion.
Answer to Problem 1P
The diameter of shaft is
Explanation of Solution
Write expression for parameter.
Here, fatigue stress concentration factor for bending is
Write expression for parameter.
Here, mid range bending moment is
Write expression for diameter by applying DE-Gerber criterion.
Here, design factor is
Conclusion:
Substitute
Substitute
Substitute
Thus, the diameter of shaft is
(b)

The diameter of shaft using DE-ASME Elliptic criterion.
Answer to Problem 1P
The diameter of shaft is
Explanation of Solution
Write expression for diameter by applying DE-Elliptical criterion.
Here, design factor is
Conclusion:
Substitute
Thus, the diameter of shaft is
(c)

The diameter of shaft using DE-Soderberg criterion.
Answer to Problem 1P
The diameter of shaft is
Explanation of Solution
Write expression for diameter by applying DE-Soderberg criterion.
Here, design factor is
Conclusion:
Substitute
Thus, the diameter of shaft is
(d)

The diameter of shaft using DE-Goodman criterion.
Answer to Problem 1P
The diameter of shaft is
Explanation of Solution
Write expression for diameter by applying DE-Goodman criterion.
Conclusion:
Substitute
Thus, the diameter of shaft is
Comparison with diameter obtained from DE-Geber Criteria.
The diameters obtain from DE-Geber Criteria is
The following table shows the comparison of the diameters obtain from different criterion with respect to DE-Gerber criteria.
Criteria | Diameter |
Percentage (Relative to DE-Geber Criteria) |
DE-Elliptical criterion | ||
DE-Soderberg criterion | ||
DE-Goodman criterion |
Want to see more full solutions like this?
Chapter 7 Solutions
Shigley's Mechanical Engineering Design (McGraw-Hill Series in Mechanical Engineering)
- A tubular shaft being designed for use on a construction site must transmit 120 kW at 1,75 Hz, The inside diameter of the shaft is to be one-half of the outside diameter. If the allowable shear stress in the shaft is 45 MPa, what is the minimum required outside diameter d?arrow_forwardRepeat Problem 11.2-3 assuming that R= 10 kN · m/rad and L = 2 m.arrow_forwardA shaft is loaded in bending and torsion such that Ma 500 lbf in, and T T = = E 600 lbf in, T = 400 lbfin, M. = 300 lbf in. For the shaft, S., 100 kpsi and S, 80 kpsi, and a fully corrected endurance limit of S, 30 kpsi is assumed. Let K, 2.2 and K, 1.8. With design factor of 2.0 determine the minimum acceptable diameter of the shaft using the (a) DE-Gerber criterion. (b) DE-elliptic criterion. (c) DE-Soderberg criterion. (d) DE-Goodman criterion. Discuss and compare the results. Harrow_forward
- A shaft is loaded in bending and torsion such that Ma = 69 N · m, Ta = 42 N · m, Mm = 52 N · m, and Tm = 31 N · m. For the shaft, Su = 700 MPa and Sy = 560 MPa, and a fully corrected endurance limit of Se = 210 MPa is assumed. Let Kf = 2.2 and Kfs = 1.8. With a diameter of 28 mm, determine the yielding factor of safety using von Mises stress to consider the possibility of static failure in the first load cycle.arrow_forwardQ2: shaft shown has: FB=0; FA=200 Ib; T=1000 Ib.in; The shaft rotating freely on bearings A and B and has reactions there (Ra,Rb); For the step take Kt =1.7 for bending and Kts= 2.2 for torsion and the material sensitivity factor is 0.8; The corrected endurance limit for the shaft material is 20 Kspi Safety factor =2 D=1.2 d Out = 140 MPa, o 70 Mpa Iield Find the small diameter d suitable for that shaft. 6 in D RA RBarrow_forwardThe disc clutch of an automobile is carried on a 2-inch 6-splined shaft and not to slide under load. The nominal dimensions are as follows: b = 0.25 D; t = 0.075 D and d = 0.85 D. The hub length of 150 % of shaft diameter. Determine the total horsepower transmitted at 3,600 rpm, if the yield strength of the shaft is 1,400 psiarrow_forward
- Q A shaft rotating at 200 r.p.m. drives another shaft at 300 r.p.m. and transmits 6 kW through a belt. The belt is 100 mm wide and 10 mm thick. The distance between the shafts is 4m. The smaller pulley is 0.5 m in diameter. Calculate the stress in the belt, if it is . An open belt drive, and 2. A cross belt drive. (Take μ = 0.3)arrow_forwardAn input shaft of a gearbox with motor power P = 7 kW and rotation number n = 1300 rpm. The diameter of an input shaft is d = 20 mm and its material is 16MnCr5. A force of F = 2800 N forces the shaft due to the operation of a gear wheel connected with a wedge on the input shaft. The distances of the gear from the bearings are given as L₁ = 40 mm and L2 = 60 mm. In the most dangerous section, you are required to check the strength according to the S = 3 safety factor. If the section is unsafe in terms of strength, what changes would you make in the design to make it safe? (The surface of the spindle is machined as fine chips, reliability poor Kg = 1.).arrow_forwardA shaft with a diameter of 51 mm rotates at 1,225 RPM. Three discs are mounted on the shaft, with weight of w, =9 N, W2= %3D 26 N and wa = 8 N, respectively, as shown in Figure below. The deflection at the corresponding mounting locations are y, = W3 = 0.179 mm, respectively. Calculate the fundamental critical speed (in RPM) using Уз 0.305 mm, y, = Y2 0.45 mm and Rayleigh's method neglecting shaft properties. Use the value of critical speed in RPM to estimate the factor of safety in terms of critical speed. Enter the factor of safety only as the answer upto 4 digits of decimal. Page 309 y3 y2 W3 W1 w2 150 350 300 100arrow_forward
- A solid shaft of 20 mm radius is transmitting 2.5 kW with the frequency of 50 Hz. Calculate the maximum shear stress. (A) Tmax (B) T max = 1.266 MPa max = 0.633 MPa (C) T (D) Tmax=0.9495 MPa = 1.899 MPaarrow_forwardDesign a typical rigid flange coupling for connecting a motor and a centrifugal pump shafts. The coupling needs to transmit 15 KW at 1000 rpm. The allowable shear stresses of the shaft, key and bolt materials are 60 MPa, 50 MPa and 25 MPa respectively. The shear modulus of the shaft material may be taken as 84GPa. The angle of twist of the shaft should be limited to 1 degree in 20 times the shaft diameter. Note: show complete handwritten solutionarrow_forwardDesign a typical rigid flange coupling for connecting a motor and a centrifugal pump shafts. The coupling needs to transmit 15 KW at 1000 rpm. The allowable shear stresses of the shaft, key and bolt materials are 60 MPa, 50 MPa and 25 MPa respectively. The shear modulus of the shaft material may be taken as 84GPa. The angle of twist of the shaft should be limited to 1 degree in 20 times the shaft diameter. Note: show complete solutionarrow_forward
- Mechanics of Materials (MindTap Course List)Mechanical EngineeringISBN:9781337093347Author:Barry J. Goodno, James M. GerePublisher:Cengage Learning
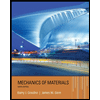