Each of the following scenarios requires the use of accountinginformation to carry out one or more of the following managerialactivities: (1) planning, (2) control and evaluation, (3) continuousimprovement, or (4) decision making.a. MANAGER: At the last board meeting, we established anobjective of earning an after-tax profit equal to 20 percent of sales.I need to know the revenue that we need to earn in order to meetthis objective, given that we have $250,000 to spend on thepromotional campaign. Once I have estimated sales in units, wethen need to outline a promotional campaign that conforms to ourbudget and that will take us where we want to be. However, tocompute the targeted sales revenue, I need to know the unit salesprice, the unit variable cost, and the associated fixed productionand support costs. I also need to know the tax rate. b. MANAGER: We have problems with our procurement process.Our accounts payable department is spending 80 percent of itstime resolving discrepancies between the purchase order,receiving order, and supplier's invoice. Incorrect part numbers onthe purchase orders, incorrect quantities ordered, and wrong partssent (or the incorrect quantity) are just a few examples of sourcesof discrepancies. A complete redesign of the process has beensuggested, which will allow us to eliminate virtually all of theerrors and, at the same time, significantly reduce the number ofclerks needed in purchasing, receiving, and accounts payable. Thisredesign promises to significantly reduce costs, decrease leadtime, and increase customer satisfaction.c. MANAGER: This overhead cost report indicates that we havespent significantly more on inspection, purchasing, andproduction than was budgeted. An investigation has revealed thatthe source of the problem is faulty components from suppliers. Asupplier evaluation has revealed that by selecting five supplierswith the best quality records (out of 15 currently used), the numberof defective components will be dramatically reduced, thusproducing significant overhead savings by reducing the demandfor inspections, reordering, and rework. d. MANAGER: A large local firm has approached me and hasoffered to sell us one of the components used in our small engines-a component that we are currently producing internally. I needto know costs that we would avoid if this component is purchasedso that I can assess the economic merits of this offer.e. MANAGER: Currently, our deluxe lawn mower is losing money.We need to increase profits. I would like to know how much ourprofits would be if we reduce our variable costs by $50 per mowerwhile maintaining our current sales volume. Also, marketingclaims that if we increase advertising expenditures by $1,000,000and cut prices by 15 percent, we can increase the number ofmowers sold by 25 percent. I would like to know which approachoffers the most profit, or if a combination of the approaches maybe best.f. MANAGER: We are implementing a major quality improvementprogram. We will be increasing the investment in prevention anddetection activities with the expectation of driving down bothinternal and external failure costs. I expect to see trend reports forall categories of quality costs. I want to see if improving qualityreally does reduce costs and improve profitability, g. MANAGER: Our engineering design department has proposed anew design for our product. The new design promises to reducepost-purchase costs and, as a consequence, increase market share.I need to know the cost of producing this new design because ituses some new components and requires some differentmanufacturing processes. I would then like to have a projectedincome statement based on the new market share and newproduction costs. The planned selling price will be the same, ormaybe even 10 percent lower. Projections based on the two pricescenarios would be needed.h. MANAGER: My engineers have said that by redesigning our twomain production processes, we can reduce move time by 90percent and wait time by 85 percent. This would decrease cycletime and virtually eliminate the need to carry finished goodsinventories. On-time deliveries would also increase dramatically.This would produce cost savings of nearly $20,000,000 per year.Market share and revenues would also increase. Required:1. Describe each of the four managerial responsibilities.2. Identify the managerial activity or activities applicable for eachscenario, and indicate the role of accounting information in theactivity.
Each of the following scenarios requires the use of accounting
information to carry out one or more of the following managerial
activities: (1) planning, (2) control and evaluation, (3) continuous
improvement, or (4) decision making.
a. MANAGER: At the last board meeting, we established an
objective of earning an after-tax profit equal to 20 percent of sales.
I need to know the revenue that we need to earn in order to meet
this objective, given that we have $250,000 to spend on the
promotional campaign. Once I have estimated sales in units, we
then need to outline a promotional campaign that conforms to our
budget and that will take us where we want to be. However, to
compute the targeted sales revenue, I need to know the unit sales
price, the unit variable cost, and the associated fixed production
and support costs. I also need to know the tax rate.
b. MANAGER: We have problems with our procurement process.
Our accounts payable department is spending 80 percent of its
time resolving discrepancies between the purchase order,
receiving order, and supplier's invoice. Incorrect part numbers on
the purchase orders, incorrect quantities ordered, and wrong parts
sent (or the incorrect quantity) are just a few examples of sources
of discrepancies. A complete redesign of the process has been
suggested, which will allow us to eliminate virtually all of the
errors and, at the same time, significantly reduce the number of
clerks needed in purchasing, receiving, and accounts payable. This
redesign promises to significantly reduce costs, decrease lead
time, and increase customer satisfaction.
c. MANAGER: This overhead cost report indicates that we have
spent significantly more on inspection, purchasing, and
production than was budgeted. An investigation has revealed that
the source of the problem is faulty components from suppliers. A
supplier evaluation has revealed that by selecting five suppliers
with the best quality records (out of 15 currently used), the number
of defective components will be dramatically reduced, thus
producing significant overhead savings by reducing the demand
for inspections, reordering, and rework.
d. MANAGER: A large local firm has approached me and has
offered to sell us one of the components used in our small engines
-a component that we are currently producing internally. I need
to know costs that we would avoid if this component is purchased
so that I can assess the economic merits of this offer.
e. MANAGER: Currently, our deluxe lawn mower is losing money.
We need to increase profits. I would like to know how much our
profits would be if we reduce our variable costs by $50 per mower
while maintaining our current sales volume. Also, marketing
claims that if we increase advertising expenditures by $1,000,000
and cut prices by 15 percent, we can increase the number of
mowers sold by 25 percent. I would like to know which approach
offers the most profit, or if a combination of the approaches may
be best.
f. MANAGER: We are implementing a major quality improvement
program. We will be increasing the investment in prevention and
detection activities with the expectation of driving down both
internal and external failure costs. I expect to see trend reports for
all categories of quality costs. I want to see if improving quality
really does reduce costs and improve profitability,
g. MANAGER: Our engineering design department has proposed a
new design for our product. The new design promises to reduce
post-purchase costs and, as a consequence, increase market share.
I need to know the cost of producing this new design because it
uses some new components and requires some different
manufacturing processes. I would then like to have a projected
income statement based on the new market share and new
production costs. The planned selling price will be the same, or
maybe even 10 percent lower. Projections based on the two price
scenarios would be needed.
h. MANAGER: My engineers have said that by redesigning our two
main production processes, we can reduce move time by 90
percent and wait time by 85 percent. This would decrease cycle
time and virtually eliminate the need to carry finished goods
inventories. On-time deliveries would also increase dramatically.
This would produce cost savings of nearly $20,000,000 per year.
Market share and revenues would also increase.
Required:
1. Describe each of the four managerial responsibilities.
2. Identify the managerial activity or activities applicable for each
scenario, and indicate the role of accounting information in the
activity.

Trending now
This is a popular solution!
Step by step
Solved in 2 steps

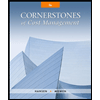
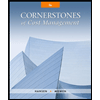